REPAIR VS. STRENGTHENING
- Customer Support
- May 1, 2013
- 3 min read
Concrete experts commonly use the terms structural repair and structural strengthening to describe building renovation activities. Although the two terms sound similar, they refer to slightly different concepts. Structural repair describes the process of reconstructing a facility or its structural elements. This process involves determining the origin of the distress, removing damaged materials and causes of distress, as well as selecting and applying appropriate repair materials that restore the integrity of the structural elements and extend the structure’s useful life.
Structural strengthening, on the other hand, is an upgrade of a building’s structural system designed to improve performance under existing loads or to increase the strength of the existing structural components to carry additional loads. For upgrade projects, design engineers must deal with structures in which every element carries a share of the existing load. The effects of strengthening or removing part or all of a structural element – such as penetrations or deteriorated materials – must be analyzed carefully to determine their influence on the global behavior of the structure. Failure to do so may overstress the structural element surrounding the repair area, which can lead to a bigger problem and even localized failure. With upgrade projects, contractors also must deal with critical issues related to access to the work area, constructability of the repair, noise and dust control, environmental impact, and the selection of construction materials.
In many cases, the original structural drawings are unavailable and an in-situ assessment of the existing structure may be required to establish member strengths and reinforcement details. Load testing can be used to verify that a structure can safely support the design loads and to verify the capacity of repaired or strengthened members.
Why Repair or Strengthen?
In general, structural deficiencies can result from code changes, seismic upgrade needs, deficiencies that develop because of environmental effects (i.e., corrosion), changes in use that increase service loads, requirements to enhance blast and ballistic resistance, or deficiencies within the structure caused by errors during original design or construction. Once this has happened, two alternatives to fixing the problem are to replace the structure or to repair and strengthen it. Economically, repair and strengthening are often the only viable solution.
There are a variety of different methods available to repair or strengthen existing buildings, including fiber reinforced polymer composites, span shortening, externally bonded steel, external or internal post-tensioning systems, and section enlargement. The technique or combination of techniques used will depend on the specific requirements of the project in regard to technical concerns (engineering), constructability issues (construction methods), aesthetics (architectural), and economics (ROI). The following gives a brief description of common repair and strengthening methods and case-study applications.
Doing It Right the First Time!
Regardless of the experience and experimental knowledge gained in more than 100 years of reinforced concrete construction, structures require repair and/or strengthening because of natural causes, deterioration, human error and change in loading conditions. But by accepting this reality, building owners can be prepared for the necessity of strengthening and repair and will be able to implement such programs before structural and safety issues become dire.
Likewise, repair contractors should also be prepared for the tasks they will undertake. Challenges usually arise because of unknown actual structural states such as load path, material properties, as well as the size and location of existing reinforcement or prestressing. The degree to which the upgrade system and the existing structural elements will share the loads must be evaluated and properly addressed in the upgrade design, detailing and implementation methods.
To design and select a repair/strengthening method and material successfully, a system concept must be employed. No matter what strengthening technique is chosen, one of the requirements of the composite system is the ability to perform as an integrated system. This goal can be achieved only by providing an adequate bond between the existing concrete and external reinforcement – creating a bond strength such that the composite structure behaves monolithically.
In addition, facility engineers should consider the procurement process for specialty repair and strengthening projects to be different from new construction services. Engaging specialty engineering and contracting firms that are familiar with the critical aspects highlighted within this article will ensure the most cost-effective and long-lasting results. Although it may appear there is an up-front financial benefit to obtaining these specialty services from firms with experience in new construction, the real risk is that the repairs will cause an endless “repair of repairs” cycle resulting in additional disruption and expenditure to owners. When it comes to structural repair and strengthening, the mantra “do it right the first time” pays dividends.
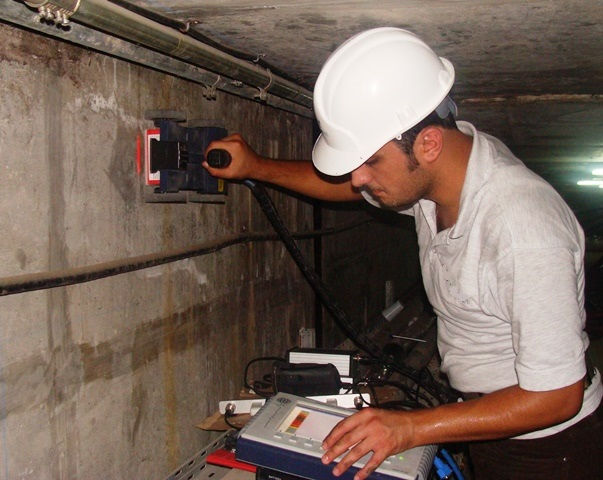
Comments